5S Certifications
5S is a workplace organizational method that uses a list of words to describe how to organize a work space. Those words are Sort, Straighten, Shine, Standardize and Sustain. 5S was originally developed in Japan as part of Just-in-Time manufacturing techniques. Now, 5S is being applied to a wide variety of industries. It has expanded from manufacturing to healthcare, education, government, and more. The 5S Concept certification, available exclusively through the Management and Strategy Institute, will give you an understanding of 5S methodology and how it is applied in the workplace.
The 5S methodology is based on five Japanese words that start with the letter "S"
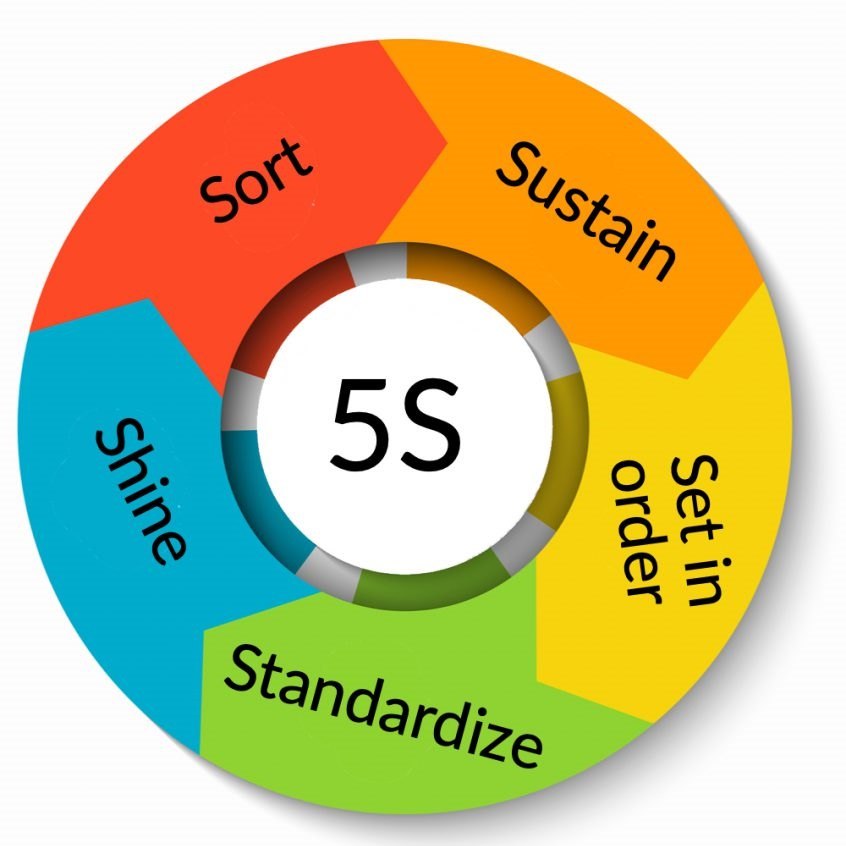
Benefits of implementing 5S
- Clean and Pleasant Environment: 5S creates an organised and clean environment. Employees love to work in a clean and pleasant workplace.
- Self Discipline: Employees acquire self-discipline, they need to maintain the standards (put the tools pack in their positions, daily cleaning, Regular Audits, etc).
- Identify and Eliminate Wastes: 5S would bring a lot of wastes to the surface (Overproduction, excess motion, etc.) Employees can start reducing the wastes and improve the Productivity
- Create More Space: removal of unwanted items and organising the necessary materials release space. We have found 5S releasing around 10% to 20% more floor space in most of our engagements.
- Identify Abnormalities: Oil Leaks, Air Leakages and Vibration of machines can be identified easily and fixed immediately.
- Improvement in Safety: 5S helps in crating a safe workplace by reducing accidents caused by Slippery floors, eliminating oil leaks and creating visual indicators.
- Improvement in Employee Morale and Positive Attitude: 5S creates a positive attitude and starts a culture change in the company. Employees starts owning the workplace and their machines and they have a sense of belongingness to the company.
Advantages
- It improves productivity;
- It improves the safety of employees and reduces the frequency of work accidents;
- It increases the quality of products;
- It reduces material loss and therefore costs;
- It improves the working environment and limits travel;
- It allows for a continuous improvement process and promotes the confidence of all stakeholders.